Quality Assurance Specialist (QAS) I - #253647
SOFIE
Date: 1 week ago
City: Haverhill, MA
Contract type: Full time
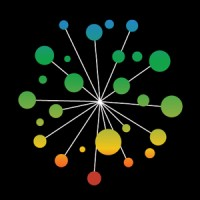
Job Description | Quality Assurance Specialist (QAS) I
Title | Quality Assurance Specialist I
Department | Quality/Regulatory/EH&S
Reports To | Regional Manager, Quality Assurance (or equivalent QA Manager)
Overview
The Quality Assurance Specialist I will be responsible for the oversight of the Quality Assurance program and the Quality Management System at the site level.
Essential Duties And Responsibilities
Maintain oversight of the QA program and Quality Management System (QMS) at a single SOFIE manufacturing facility producing products under both 21 CFR Part 212 and 211 (as needed) regulations.
Apply quality assurance processes and procedures at the site level to ensure product quality and regulatory compliance.
Strong collaboration, including problem solving and continuous improvement efforts, and communication with the Facility Manager and Operations team.
Write, review, approve, and implement procedures, specifications, processes, and methods as required.
Oversee the examination and evaluation of each lot of incoming material before use to ensure that the material meets its established specifications.
Ensure that components, containers, closures, in-process materials, packaging materials, labeling, and finished dosage forms are examined and approved or rejected to ensure that all these meet their current specifications.
Ensure that personnel are properly trained and qualified. Ensure that the training is documented.
Conduct periodic audits of the site to monitor compliance with established procedures and practices. May infrequently audit another site.
Liaise with internal and external inspectors and representatives, particularly on QA-related topics.
Oversee the metrology program at the site (i.e., equipment, personnel qualifications, validations, etc.).
Ensure manufacturing and analytical equipment is appropriately maintained and calibrated. Ensure applicable facility certifications are maintained. Identify to management problems in personnel, equipment, and the facility that require correction.
Review documents associated with the site’s QA program for completeness, errors, and omissions. Review executed CGMP records and product batch records to ensure compliance and product quality.
Review trends (e.g., environmental monitoring, deviations, facility issues, etc.) to initiate corrective and preventive actions and/or for continuous process improvement.
Conduct continuous review of aseptic operations to ensure compliance to internal procedures (e.g., owning, cleaning, sanitation, sterility, environmental monitoring, etc.) and USP/FDA regulations.
Ensure any deviations from normal procedures are documented and justified.
Ensure an investigation is performed and documented when required, and corrective and preventative actions are taken (i.e., follow and maintain corporate CAPA, deviation, and OOS protocols).
Ensure compliance to all applicable standard operating procedures and regulations, including 21 CFR Part 212 (and 211 as needed) requirements.
Ensure product complaints are managed in a manner consistent with Company SOPs and FDA regulations.
Responsible for opening change controls and initiating, maintaining, and reviewing SOFIE network and site-specific procedures relative to their job functions.
Oversee the site-level change control process. Ensure that changes in the laboratory are accepted or rejected as appropriate, and ensure the changes are appropriately documented.
Attend quality and operational meetings. Interface with Corporate QA and Operations on quality related issues. Provide status updates as required management.
Expected extensive knowledge of up to two SOFIE products
Qualifications
Other responsibilities as required.
Bachelor’s Degree (Scientific / Medical / Quality), at minimum, preferred.
Experience and/or full knowledge of manufacturing operations, preparation of sterile injectables, aseptic processing, and distribution of aseptic products preferred.
Quality, Pharmacy, Or CGMP Manufacturing Experience Preferred.
Knowledge of USP, FDA, and cGMP regulations preferred.
Knowledge of how and ability to write, review, and revise SOPs required.
Ability to read, analyze, and interpret governmental regulations, general business periodicals, professional journals, or technical procedures required.
Ability to read and interpret documents such as safety rules, operating and maintenance instructions, and procedure
manuals required.
Ability to write reports, business correspondence, and procedure manuals required.
Ability to effectively present information, deliver training, and respond to questions from groups of managers, clients,
customers, and the general public required.
Ability to define problems, collect data, establish facts, and draw valid conclusions required.
Ability to solve problems and handle issues required.
Proficient in MS Office applications required.
Strong interpersonal communication skills for interacting with site personnel, inspectors, and internal and external vendors required.
Requirements For Quality Assurance Specialist (QAS) I
Associate’s or Bachelor’s Degree, at minimum
Relevant certifications and/or experience may be substituted in lieu of this requirement
1-2 years of QA, Pharmacy, and/or CGMP manufacturing experience
Title | Quality Assurance Specialist I
Department | Quality/Regulatory/EH&S
Reports To | Regional Manager, Quality Assurance (or equivalent QA Manager)
Overview
The Quality Assurance Specialist I will be responsible for the oversight of the Quality Assurance program and the Quality Management System at the site level.
Essential Duties And Responsibilities
Maintain oversight of the QA program and Quality Management System (QMS) at a single SOFIE manufacturing facility producing products under both 21 CFR Part 212 and 211 (as needed) regulations.
Apply quality assurance processes and procedures at the site level to ensure product quality and regulatory compliance.
Strong collaboration, including problem solving and continuous improvement efforts, and communication with the Facility Manager and Operations team.
Write, review, approve, and implement procedures, specifications, processes, and methods as required.
Oversee the examination and evaluation of each lot of incoming material before use to ensure that the material meets its established specifications.
Ensure that components, containers, closures, in-process materials, packaging materials, labeling, and finished dosage forms are examined and approved or rejected to ensure that all these meet their current specifications.
Ensure that personnel are properly trained and qualified. Ensure that the training is documented.
Conduct periodic audits of the site to monitor compliance with established procedures and practices. May infrequently audit another site.
Liaise with internal and external inspectors and representatives, particularly on QA-related topics.
Oversee the metrology program at the site (i.e., equipment, personnel qualifications, validations, etc.).
Ensure manufacturing and analytical equipment is appropriately maintained and calibrated. Ensure applicable facility certifications are maintained. Identify to management problems in personnel, equipment, and the facility that require correction.
Review documents associated with the site’s QA program for completeness, errors, and omissions. Review executed CGMP records and product batch records to ensure compliance and product quality.
Review trends (e.g., environmental monitoring, deviations, facility issues, etc.) to initiate corrective and preventive actions and/or for continuous process improvement.
Conduct continuous review of aseptic operations to ensure compliance to internal procedures (e.g., owning, cleaning, sanitation, sterility, environmental monitoring, etc.) and USP/FDA regulations.
Ensure any deviations from normal procedures are documented and justified.
Ensure an investigation is performed and documented when required, and corrective and preventative actions are taken (i.e., follow and maintain corporate CAPA, deviation, and OOS protocols).
Ensure compliance to all applicable standard operating procedures and regulations, including 21 CFR Part 212 (and 211 as needed) requirements.
Ensure product complaints are managed in a manner consistent with Company SOPs and FDA regulations.
Responsible for opening change controls and initiating, maintaining, and reviewing SOFIE network and site-specific procedures relative to their job functions.
Oversee the site-level change control process. Ensure that changes in the laboratory are accepted or rejected as appropriate, and ensure the changes are appropriately documented.
Attend quality and operational meetings. Interface with Corporate QA and Operations on quality related issues. Provide status updates as required management.
Expected extensive knowledge of up to two SOFIE products
Qualifications
Other responsibilities as required.
Bachelor’s Degree (Scientific / Medical / Quality), at minimum, preferred.
Experience and/or full knowledge of manufacturing operations, preparation of sterile injectables, aseptic processing, and distribution of aseptic products preferred.
Quality, Pharmacy, Or CGMP Manufacturing Experience Preferred.
Knowledge of USP, FDA, and cGMP regulations preferred.
Knowledge of how and ability to write, review, and revise SOPs required.
Ability to read, analyze, and interpret governmental regulations, general business periodicals, professional journals, or technical procedures required.
Ability to read and interpret documents such as safety rules, operating and maintenance instructions, and procedure
manuals required.
Ability to write reports, business correspondence, and procedure manuals required.
Ability to effectively present information, deliver training, and respond to questions from groups of managers, clients,
customers, and the general public required.
Ability to define problems, collect data, establish facts, and draw valid conclusions required.
Ability to solve problems and handle issues required.
Proficient in MS Office applications required.
Strong interpersonal communication skills for interacting with site personnel, inspectors, and internal and external vendors required.
Requirements For Quality Assurance Specialist (QAS) I
Associate’s or Bachelor’s Degree, at minimum
Relevant certifications and/or experience may be substituted in lieu of this requirement
1-2 years of QA, Pharmacy, and/or CGMP manufacturing experience
How to apply
To apply for this job you need to authorize on our website. If you don't have an account yet, please register.
Post a resumeSimilar jobs
Automotive Parts Manager
Jaffarian Volvo Toyota,
Haverhill, MA
1 day ago
Jaffarian Automotive is seeking an experienced candidate to manage our parts operation. We are looking for someone with hands on skills and the dedication to lead our team to the next level. Responsibilities Ensures that all employees follow their assigned work schedules and adhere to the absenteeism, reporting and tardiness policy Forecasts goals and objectives for the department and strives...
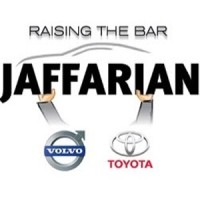
LPN Continuous Skilled Nursing, Merrimack Valley Area- Home Care
Northeast Clinical Services,
Haverhill, MA
5 days ago
Back to Job Openings LPN Continuous Skilled Nursing, Merrimack Valley Area- Home Care Haverhill MA Posted 2 weeks ago Apply Share NortheastArc-Clinical Services is a nonprofit Medicaid/Medicare-certified home healthcare agency founded in 2003 . Our mission is to serve medically fragile pediatric and adult populations in cities and towns across Bristol, Essex, Middlesex, Norfolk, Plymouth, and Suffolk Counties. Job Openings...
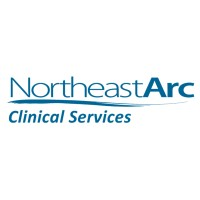
Salesperson/Store Driver Store 6251
Advance Auto Parts,
Haverhill, MA
1 week ago
Job Description What is a Salesperson? Entry level sales position capable of supporting the DIY business and achieve our sales and service objectives. The role has good knowledge of store systems, basic automotive system knowledge and basic part knowledge. The role has the basic ability to source from stores, hubs, pdq, and external suppliers. The role has in-depth knowledge of...
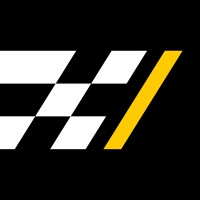